2018-02-22
Operating Principle of an Oxygen Monitor
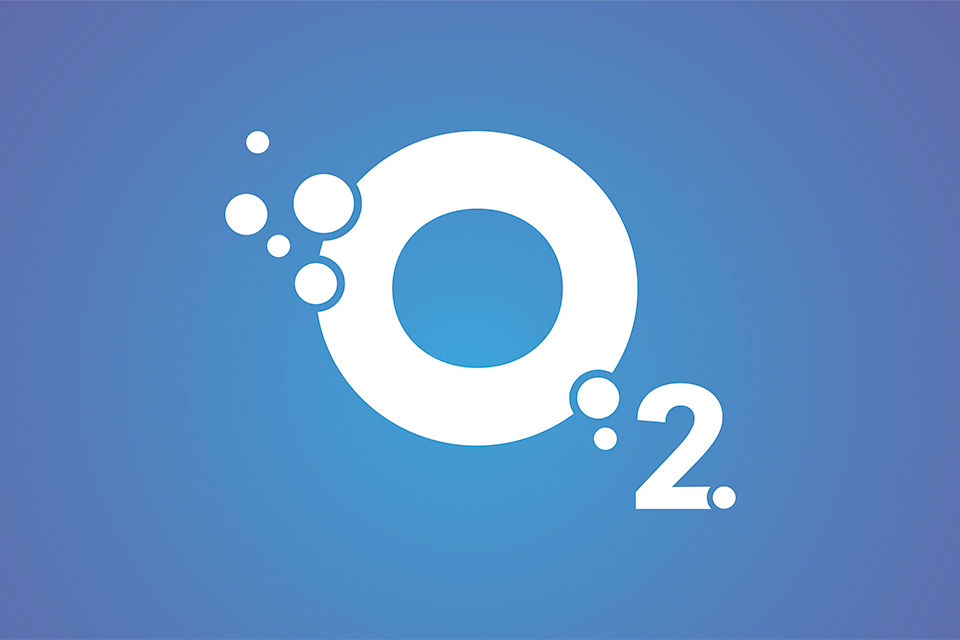
The oxygen concentration in the flue gas of a combustion process such as that of a power plant or a waste incinerator gives a good indication of the efficiency of the combustion process. The parameter is therefore of great interest to optimize fuel economy, but also to control and reduce emissions of air pollutants.
An ideal combustion process only results in CO2 and water, but if the air supply is too low you get unburnt fuel, which both is bad for the economy and produces undesirable emissions of e.g. CO and hydrocarbons. Effectively, you therefore wish to run the combustion with a slight excess of oxygen in the flue gas, indicating enough air supply to the furnace securing complete combustion.
The Zirconia Method
The traditional method of measuring oxygen content in the flue gas makes use of a zirconia cell. Zirconia is a very stable and durable ceramic material, consisting of the crystalline oxide of Zirconium, chemical formula ZrO2. One side of the cell is exposed to oxygen of a known concentration, normally ambient air, while the other side of the cell is exposed to the flue gas. The difference in oxygen concentration between the two sides gives rise to an electrochemically induced voltage which depends on the oxygen concentration difference. The voltage is measured and converted to an oxygen concentration reading.
In large-scale industrial processes, the challenge is often to design the probe to withstand the often harsh environment of the often high temperature, dust-laden, and corrosive flue gas. Careful selection of probe material and dust deflection/purging might be required to make the probe durable enough.
The Optical Method
There are also other ways to monitor oxygen than using zirconia sensors. One alternative is absorption spectroscopy utilizing a laser diode as light source. Much like the DOAS technology, a detector senses the “fingerprint” of the oxygen molecules along a monitoring path. The amount of absorption gives the oxygen concentration. At the same time, it is often possible to calculate the temperature very accurately. This kind of oxygen monitors are non-intrusive, and therefore very suitable for extremely tough environments with reactive flue gases and very high temperatures, where zirconia cells would not last for long.
Keeping track of the oxygen content is an important tool for optimizing combustion processes. The operating environment of such sensor can be a challenge, but there is usually still an oxygen monitor for every need.